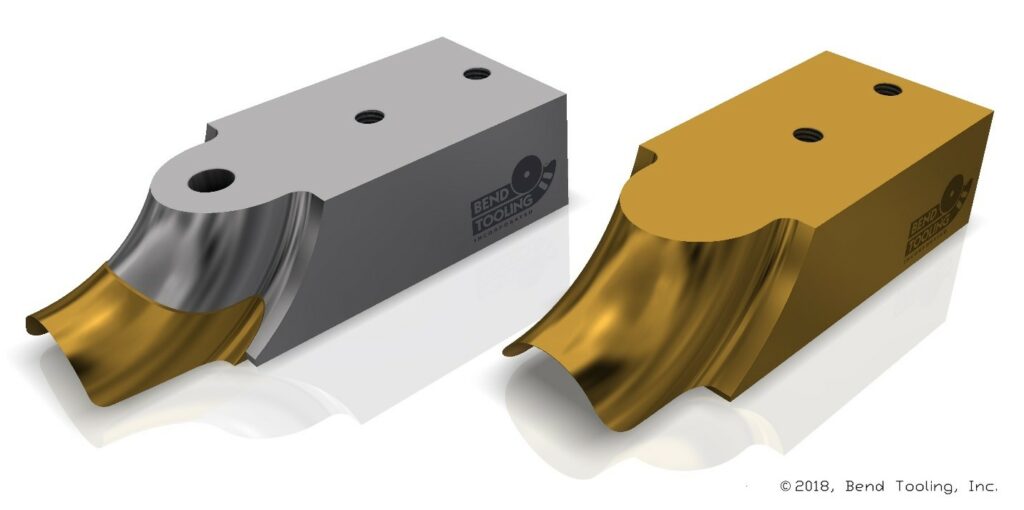
Two main categories of wiper die are inserted (left) and full body (right). The inserted variety has a replaceable tip. A full-body wiper die can handle more severe bending applications than an inserted wiper, but the additional capability comes with additional cost.
When your next rotary draw bending application calls for a wiper die, you might want to think twice about which type of wiper you should use. The purpose of a wiper die is straightforward: filling the gap between the tube and the bend die, opposite the pressure die, to prevent material from bunching up behind the bend. That is, it helps to make the perfect bend that you are determined to achieve. However, there are a few things to consider before specifying a wiper die—a simple but potentially costly task.
Since the wiper die works primarily as a bearing surface against the tube, it is subject to continuous wear and must be replaced when it becomes worn beyond function. So when tooling up for production on your tube bender, selecting the wiper die is a critical decision.
Types of Wiper Dies
The two fundamental types of wiper dies are solid body and inserted. Both types function the same way, but each has its advantages.
A solid-body wiper die is a made from a solid piece of material, usually aluminum-bronze (to bend stainless steel, titanium, INCONEL® alloy, or mild steel tubing) or hard-chrome-plated steel (to bend aluminized or aluminum tubing). Standard features include a mounting pattern to match the machine’s mounting requirements, a tube cavity, and a radius face to match the radius block for its specific application (see Lead Image).
An inserted wiper die has the same features as a solid-body wiper, but it is composed of a steel wiper-holder that uses a replaceable wiper tip insert that extends throughout the critical wear surfaces of the wiper die. Wiper inserts generally are made from the same material varieties as their solid-body counterparts.
Solid-body wiper dies often are preferred for thin-wall, tight-radius applications because of their lengthy, uninterrupted bearing surface. Furthermore, their substantial radius face provides a significant amount of contact area with the bend die for added support. These attributes allow them to perform well under a high amount of bending pressure. However, these benefits come at a premium in that they are subject to higher initial, maintenance, and replacement costs.
Inserted wiper dies are suitable for most applications. Unlike solid wipers, tips made from various materials may be used to work with a single tip holder, depending on the material being bent. Because inserted wiper holders are not replaced on a regular basis, it can be cost-effective to incorporate design features that aren’t feasible for solid wiper tooling, which must be replaced more frequently. Such features include relief for close-collet approach and custom lubrication ports. Replacement wiper tips are inexpensive and are suitable for moderate to high-volume production applications. Furthermore, in most cases, the wiper insert may be replaced without having to remove and reset the wiper holder’s established position.
Another important aspect of wiper tooling that often is overlooked is the wiper tip or feathered edge geometry. The feathered edge design is perhaps the most critical consideration when selecting the right type of wiper for the job because it supports the region of the tube that has the biggest impact on bend quality, and it also affects how the wiper die is permitted to be positioned.
The primary role of the wiper is to work in conjunction with the mandrel to help contain the tube wall at the intrados (the inside radius of the bend), which forces it to thicken rather than wrinkle. The application’s dependence on the wiper’s ability to provide support is largely based on the amount of material compression that occurs at the intrados. The simplest way to predict the amount of compression is to look at the D of bend, which is the application’s centerline radius (CLR) divided by the tube’s outside diameter. For example, a 3-inch diameter tube that is to be bent on a 3-inch CLR would be considered a 1D application; the compression that will occur in a 1D application is 50 percent. In other words, as the material flows during the bending process, quite a bit of it will accumulate at the intrados; preventing wrinkles in this region means that the wall thickness will increase by 50 percent.
Such an increase in wall thickness highlights the amount of work that a wiper die may be tasked to handle in an extreme application. The two types of feathered edge geometry that are commonly offered are standard geometry and offset geometry.
The feathered edge of a standard-geometry wiper is such that if it is seated fully against the bend die with zero rake angle, or completely parallel to the tube, the very tip of the wiper will extend to the line of tangency on the bender (see Figure 1). In many cases, if the tip of the wiper is positioned at tangent, it may become pinched between the bend die and the tube. The results of such a setup position range from achieving acceptable bend quality to substantial tearing of the wiper tip, often to such an extreme that it is no longer usable. For this reason a standard-cut wiper should be raked to rotate the wiper tip back away from tangent. This prevents pinching the wiper tip but also reduces the amount of support that the wiper cavity is able to provide to the tube.
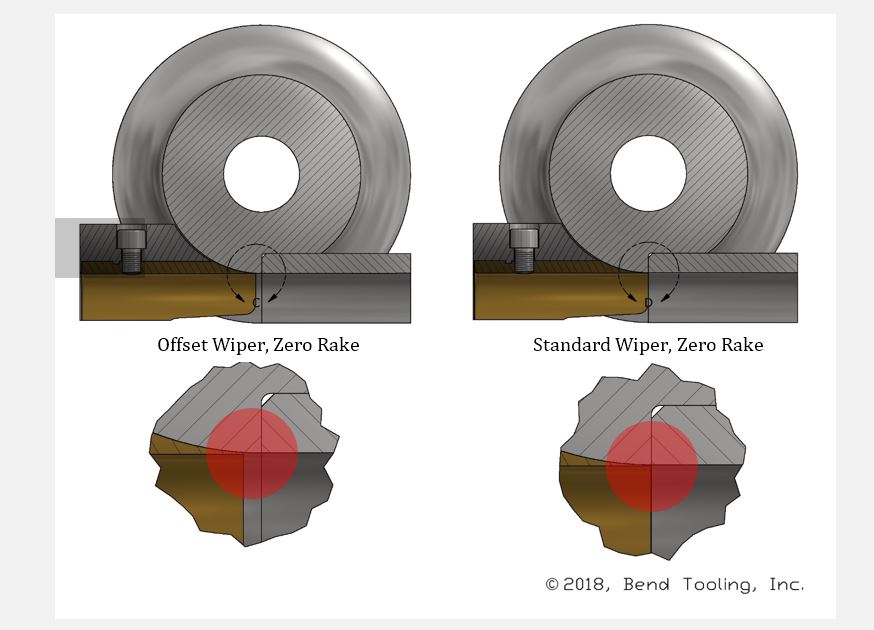
Figure 1
Standard wipers often are used for applications that require less support to prevent wrinkles from forming behind the bend, such as any bend with a radius greater than 1.5D. Since these types of wipers are traditionally raked, they tend to exhibit signs of wear throughout their lifetime: a reduction in rake angle will compensate for such wear.
Offset-geometry feathered edge wipers, commonly known as aero style, provide more support than a standard wiper, especially for tight-radius bending applications. An aero wiper may be set without rake while remaining fully seated against the bend die cavity. When set correctly, the aero wiper tip will set just behind tangent to eliminate pinching or tearing of the tip. The radius face of the wiper makes full contact with the bend die cavity to provide maximum stability, while the wiper die cavity, parallel to the tube, provides full support to the unbent section of tube throughout its entire length.
Aero wipers are suitable for applications with a CLR of 1.5D or less and for all applications that require little or no rake angle. This tooling tends to wear more gradually than standard wipers, with little or no adjustment required. This is especially beneficial in high-volume applications in which wiper insert replacement is preferred over repeated adjustment and subsequent resetting.
Your Best Bet
The next step is to decide which type of wiper die is most suitable for your application.
First, reviewing your machine’s wiper mounting configuration is a critical step that often is overlooked. Conventional tube bender designs use wiper mounting systems that allow the wiper to be raked, or angled away from the tube, as desired, but many mounting systems do not offer this option. If not, consider using an aero-cut wiper.
Although wiper die selection tables are available online, your application’s wall factor—the tube’s diameter divided its wall thickness—can help you determine if you need a solid-body wiper. If the wall factor exceeds 60, a solid-body wiper die is most likely your best option.
Some other considerations can influence your decision as well. If your application’s production volume is relatively low, less than 1,000 bends per year, and if the setup often is changed over to other sizes, it makes sense to settle on solid tooling because the wiper die likely won’t see nearly as much wear as it would in higher-volume applications. Furthermore, solid-body wiper dies tend to compensate for other aspects of the setup that are lacking, often resulting in lower setup waste. If you’re on the fence about a more difficult, but high-volume job, it’s worth taking a serious look at using the inserted style as your wiper of choice. The potential cost savings could pay off in a big way.
Because inserted wiper tooling has both a lower initial cost and subsequent maintenance costs, it makes the most sense to use it for all applications with a wall factor lower than 60, regardless of the production volume.
Plan for Wear
The bottom line is that either type of wiper die will likely get you up and running for most applications. At some point the wiper die will become worn or damaged beyond function and must be replaced.
The cost and lead time of a replacement solid-body wiper die, or the required time-frame to send out an existing wiper for refurbishment, are worth considering before making a decision. In comparison, launching your next bending application with an inserted wiper die and a few replacement wiper inserts would make this process as simple as changing out the wiper tip.
Frequently Asked Questions
1. What is the main purpose of a wiper die in tube bending?
The main purpose of a wiper die is to fill the gap between the tube and the bend die, opposite the pressure die. This prevents the tube material from bunching up or wrinkling behind the bend, helping you achieve a perfect bend.
2. What are the two main types of wiper dies, and what’s the key difference between them?
The two fundamental types of wiper dies are solid body and inserted. The key difference is that an inserted wiper die has a replaceable tip, while a solid-body wiper die is made from a single piece of material.
3. When should I choose a solid-body wiper die over an inserted one, and vice-versa?
Solid-body wiper dies are often preferred for challenging applications like thin-wall, tight-radius bends or when performing under high bending pressure, especially if the tube’s wall factor exceeds 60. They can also be good for low-volume production (under 1,000 bends per year) because they’ll experience less wear and can compensate for other setup shortcomings.
Inserted wiper dies are generally more cost-effective for most applications, especially those with a wall factor lower than 60, regardless of production volume. They’re also ideal for moderate to high-volume production because their tips are inexpensive and can be replaced without removing the holder.
4. What is “feathered edge geometry” and why is it important for a wiper die?
Feathered edge geometry refers to the design of the wiper die’s tip, which is a critical consideration. This tip supports the inside radius of the tube where material compresses, helping to prevent wrinkles. It also affects how the wiper die can be positioned, including its “rake” (angle) relative to the tube.
5. What are the differences between standard and offset (aero-style) feathered edge geometries?
A standard-geometry wiper is designed so its tip extends to the line of tangency when set with zero rake, often requiring it to be “raked” back to prevent pinching. These are best for bends with a radius greater than 1.5D and wear gradually, allowing for rake adjustment.
An offset-geometry (or aero-style) wiper provides more support, especially for tight-radius bends (1.5D or less). It can be set with little or no rake, positioning its tip just behind the line of tangency to prevent pinching. Aero wipers tend to wear more gradually and require less adjustment, making them beneficial for high-volume jobs where insert replacement is preferred.